A23 Mechanical solid liquid slurry separation
Last Update:
Measure | Sector | Net Effect | Impact | Reliability | Tech. rqmt. | |||||
---|---|---|---|---|---|---|---|---|---|---|
NH3 | N2O | NOx | Nr to water | N2 | ||||||
A23 Mechanical solid liquid slurry separation | Sector Livestock farming | Net Effect 2 | NH3 2 | N2O 2 | NO2 | Nr to water | N2 2 | Reliability Promising | Tech. rqmts. High |
Overview
Slurry consists of both solid and liquid components, with the liquid portion containing ammonium-rich compounds that can volatilise as ammonia via the hydrolysis of urea, facilitated by urease in faeces. By mechanically separating the slurry into solid and liquid fractions, a liquid portion is obtained that contains more ammonium and decomposes more slowly (Figure 1). This ammonium-rich liquid is more efficiently absorbed by the soil when applied, leading to reduced ammonia emissions (UNECE, 2015; European Commission, 2017). The solid fraction can be used as a slow-release fertiliser or as feedstock for biogas production (Bittman et al., 2014; Sutton et al., 2022). This measure shares similarities with ‘Immediate Segregation of Urine and Faeces’; both involve separating urine from faeces. However, whilst the former targets urea hydrolysis to reduce ammonia emissions, this measure is more oriented towards enhancing nutrient utilisation and optimising land application, rather than solely preventing urea hydrolysis.
The mechanical separation of the slurry results in a stackable solid fraction and a more fluid liquid fraction, thus facilitating the handling of the slurry (European Commission, 2017). Mechanical manure separation may be used where the cost of transporting manure to the place of application is not justifiable and/or in areas where manure application must be reduced (European Commission, 2017). Following separation, organic matters, organically bound nitrogen (and phosphorus) remain mainly in the solid phase and soluble mineral nitrogen and potassium remains mostly in the liquid phase. Therefore, the liquid fraction can be better matched to the nutrient requirements of the crop plants. The solid fraction consists of coarse fibrous material and can be treated as solid manure. Nutrients and organic matter are concentrated there. It can be easily transported and used as fertiliser on distant areas or otherwise (composting, drying, pelleting, biogas substrate) (European Commission, 2017). To avoid increased ammonia, nitrous oxide and methane emissions from the solid fraction covers should be used during storage.
Possible devices for manure separation are press screws, decanter centrifuges, sieves and sieve belt presses; separation can be improved by coagulants and flocculants (Burton, 2007; UNECE, 2015; European Commission, 2017). Usually several separation processes are necessary to obtain a clarified liquid and highly concentrated solid fraction. If the size of the solids in the slurry is heterogeneous, a combination of several separation systems can be used. A high dry matter content of the slurry leads to a better separation result (European Commission, 2017).
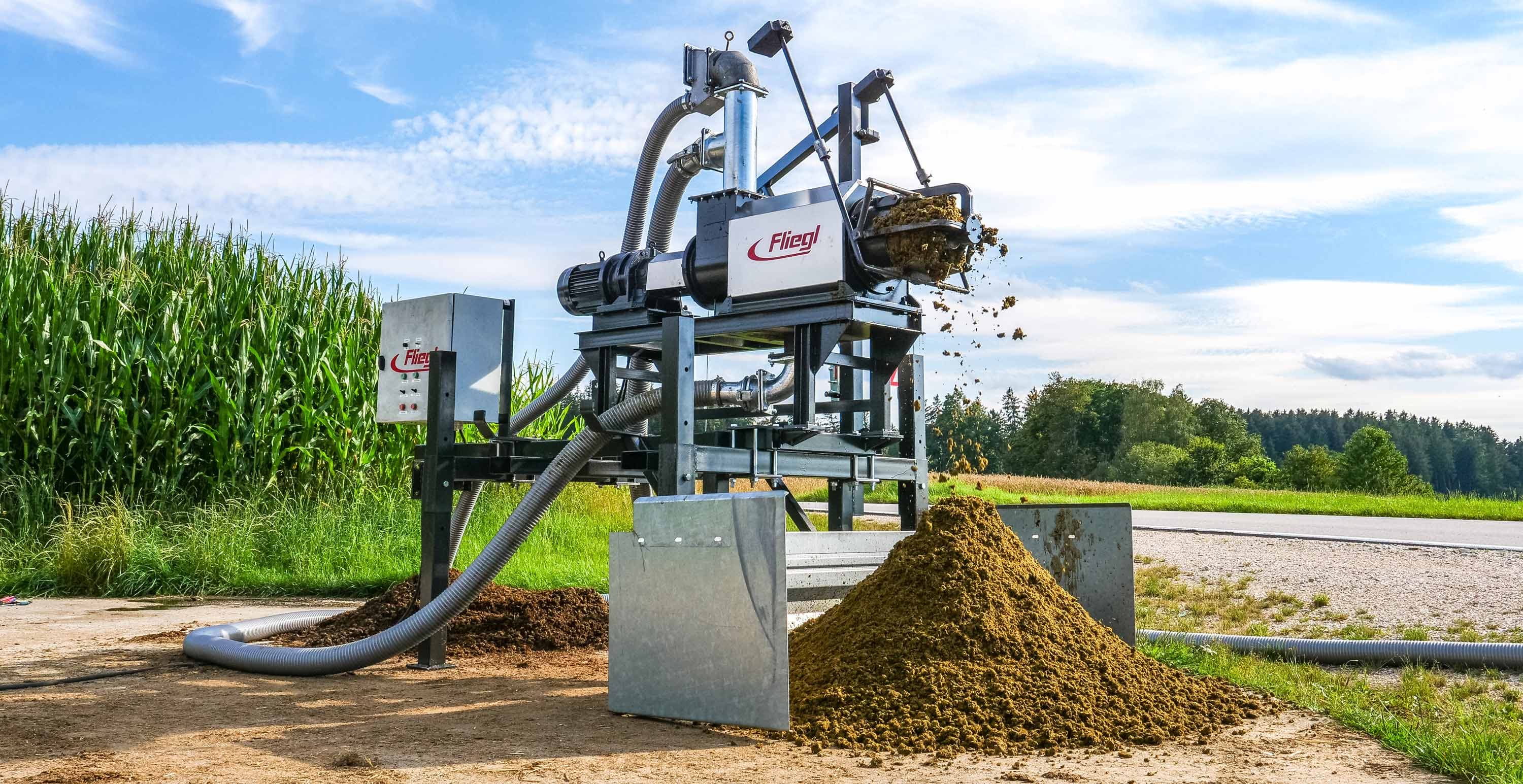
Figure 1: Solid-liquid separation of slurry using a screw press system. Picture source: https://agro-center.de/news-guelleseparator/
Measure Efficiency
Mechanical slurry separation does not directly benefit the environment (European Commission, 2017). However, it helps enable many sustainable nutrient practices, such as better manure and slurry storage, precise nutrient application, and improved nutrient management at larger scales due to the creation of more transportable products. In a review of manure storage measures, Kupper et al., (2020) found that for cattle manures, the average ammonia emissions during storage from the liquid fraction were an average of 23% higher across 12 studies, as compared to untreated cattle slurry. However, for pig slurry, only a slight effect of solid-liquid separation on ammonia release (1% increase across 7 studies) was observed and was statistically insignificant. These losses can be reduced with appropriate storage.
The reduction on ammonia emissions is delivered at the ‘soil application’ stage following appropriate storage (European Commission, 2003). The mechanical division between solid and liquid portions within slurry generates a liquid enriched with ammonium. This can lead to lowered ammonia emissions when applied to soils as it permeates soil more efficiently, offering consistent fertilisation advantages that bolster crop yields and enable a decrease in mineral nitrogen fertiliser application. Through efficient separation (screen size 1-3 mm), the ammonia emissions during the application of the liquid effluent with a low dry matter content can be reduced by 50%, due to accelerated infiltration (UN/ECE, 2014 and 2015).
However, caution must be taken to prevent ammonia and methane losses from the solid fraction, which could potentially act as a gradual-release fertiliser or serve as a feedstock for biogas production (Sutton et al., 2022).
How to implement
Various types of equipment are available for mechanically separating solid and liquid components within slurry (many summarised in Burton, 2007; UNECE, 2015; European Commission, 2017). Press screws utilise rotating screws to exert pressure, extracting liquid from solids, while centrifuges employ centrifugal force to differentiate components based on density. Screens of different mesh sizes physically divide larger solid particles from liquid. Decanter centrifuges integrate rotating bowls and screw conveyors to facilitate continuous separation, while sieve belt presses utilise belts and sieves to expel liquids from solids. Hydrocyclones generate centrifugal force through vortex motion, rotary drum filters feature rotating drums with filter mediums to separate components, and settling tanks allow for natural settling and collection. Belt filters and vibrating screens employ belts or vibration to conduct separation, while filter presses utilise pressure between filter plates. Rotary vacuum filters integrate a rotating drum with a vacuum for separation. The suitable choice of equipment depends on factors such as slurry characteristics, desired efficiency, and operational scale. Nevertheless, common steps are shared across various technology types, encompassing the subsequent procedures.
- Assess Feasibility and Need: Evaluate the cost-effectiveness of transporting manure and the availability of land for application. Determine if reducing nitrogen and phosphorus content is necessary and aligns with the goals of the operation.
- Select Appropriate Equipment: Research and choose separation equipment that suits the needs of the operation (stationary or mobile). Consider maintenance requirements and its effectiveness in reducing nutrient content.
- Determine Installation Location: Identify a suitable site for installing the equipment. Take into account accessibility, proximity to manure sources, and potential odour concerns.
- Install and Calibrate Equipment: Follow manufacturer guidelines for proper installation. Calibrate the equipment to ensure optimal separation and nutrient reduction.
- Implement Operation and Monitoring: Begin operating the separation system and closely monitor its performance. Ensure that solid and liquid fractions are effectively separated.
- Separate and Manage Fractions: Manage solid and liquid fractions separately. Store each fraction in designated areas to prevent contamination.
- Use Covers and Rapid Incorporation: During storage, cover the solid fraction to prevent NH3 and N2O emissions. When applying the solid fraction, ensure rapid incorporation to reduce emissions.
- Consider Regulations: Adhere to local regulations regarding manure storage, application, and nutrient management. Confirm that nutrient content complies with regulatory requirements.
- Regular Maintenance and Adjustment: Perform routine equipment maintenance and servicing. Continuously monitor the process and make adjustments as needed.
- Assess Field Application Options: Evaluate the suitability of the solid fraction for field spreading. If local regulations permit and the fraction's nutrient content aligns, create a plan for responsible application.
- Keep Records and Report: Maintain accurate records of the separation process, nutrient content, and emission reduction measures. These records can aid in compliance, tracking outcomes, and informed decision-making.
By following these steps, an operation can effectively implement mechanical solid/liquid separation of slurry to support better nitrogen management, reduce nitrogen emissions, and enhance overall nutrient utilisation, while considering the specific considerations provided.
Benefits
Liquid slurry separation measures can offer a range of benefits, contributing to improved efficiency, reduced environmental impact, and enhanced operational performance. Here are the benefits of adopting such measures:
Overall, the adoption of mechanical solid/liquid slurry separation measures can lead to a more sustainable, efficient, and environmentally responsible operation, enhancing both economic and operational performance.
Costs
Captial Costs
The implementation of Zeolite and/or biochar additives to adsorb slurry ammonium incurs certain capital costs that are important to consider for successful application.
The capital costs of mechanical solid/liquid slurry separation systems can vary widely depending on several factors such as the scale of the operation, the type of equipment used, the specific separation technology employed, and the local market conditions.
Mechanical solid/liquid slurry separation involves processes like filtration, centrifugation, sedimentation, and other separation methods to separate solid particles from liquid solutions or suspensions. The capital costs typically include expenses related to purchasing equipment, installation, infrastructure, and initial setup. Here are some factors that can influence the capital costs:
Given the wide range of variables that influence the capital costs of mechanical solid/liquid slurry separation systems, it's recommended to consult with equipment manufacturers, engineering firms, or industry experts to get a more accurate estimate tailored to the specific project and location. Additionally, cost estimation tools and databases specific to the industry can also provide valuable insights into capital cost ranges.
Operational Costs
The operational costs of mechanical solid/liquid slurry separation systems can encompass various ongoing expenses required to operate and maintain the separation process. These costs are incurred regularly to ensure the efficient and effective functioning of the separation equipment and associated processes. Operational costs associated with implementing this measure may include the following:
To manage operational costs effectively, operators of mechanical solid/liquid slurry separation systems should implement proactive maintenance practices, optimise process parameters, invest in employee training, and consider energy-efficient technologies. Regular monitoring and analysis of operational costs can help identify opportunities for cost reduction and process improvement.
Risks
The risks associated with mechanical separation of solid and liquid components of manure/slurry as a measure for better nitrogen management include the following:
To mitigate these risks, proper equipment selection, operational practices, nutrient management planning, and adherence to environmental regulations are essential. Regular monitoring and adjustment of separation processes can help ensure the desired benefits of improved nitrogen management are achieved without compromising environmental and agricultural outcomes.
References
Bittman, S., M. Dedina, C.M. Howard, O. Oenema, and M.A. Sutton, editors. 2014. Options for Ammonia Mitigation: Guidance from the UNECE Task Force on Reactive Nitrogen. Centre for Ecology and Hydrology, Edinburgh, UK.
Burton, C.H. 2007. The potential contribution of separation technologies to the management of livestock manure. Livest. Sci. 112(3): 208–216. doi: 10.1016/j.livsci.2007.09.004.
European Commission. 2003. Reference Document on Best Available Techniques for Intensive Rearing of Poultry and Pigs. Integr. Pollut. Prev. Control.
European Commission. 2017. Best Available Techniques (BAT) Reference Document for the Intensive Rearing of Poultry or Pigs. Ind. Emiss. Dir. 2010/75/EU (Integrated Pollut. Prev. Control. https://op.europa.eu/en/publication-detail/-/publication/f673b352-62c0-11e7-b2f2-01aa75ed71a1/language-en.
Kupper, T., C. Häni, A. Neftel, C. Kincaid, M. Bühler, et al. 2020. Ammonia and greenhouse gas emissions from slurry storage - A review. Agric. Ecosyst. Environ. 300: 106963. doi: 10.1016/j.agee.2020.106963.
Sutton, M., C. Howard, K. Mason, W. Brownlie, and Cm. Cordovil, editors. 2022. Nitrogen Opportunities for Agriculture, Food & Environment. UNECE Guidance Document on Integrated Sustainable Nitrogen Management. UK Centre for Ecology & Hydrology, Edinburgh, UK.
UNECE. 2015. Framework Code for Good Agricultural Practice for Reducing Ammonia Emissions. https://unece.org/environment-policy/publications/framework-code-good-agricultural-practice-reducing-ammonia.
Authors
Gabriele Borghardt
German Environment Agency, Germany
Will Brownlie
UK Centre for Ecology and Hydrology, Scotland